THE SCULPTING PROCESS
As an artist, I am acutely aware of my visual surroundings, with particular interest in people as subject matter. Whether watching competitive tennis, enjoying an evening at the ballet, observing children at play who are chasing, teasing, and laughing, or taking in the unconscious gestures of a person in line who is talking on the cell phone. These are the images that inspire me to create three-dimensional forms of the human figure.
Getting Started
Working from visual memory, imagination and inspiration, I sketch, photograph or videotape the model in the desired position or gesture.
Much critical thought and creativity go into this stage of the process. Ideally, working from the live model is preferred, but it is often difficult to secure the pose for extended periods. Careful notes, detail sketches, and measurements are recorded to ensure life-like proportions and likeness of the model.
Working in Clay
If the sculpture is commissioned of a loved one, athlete, dancer, group of kids or the like, and is to be cast in bronze, an initial small clay sketch, or maquette is made to scale using an aluminum wire armature (to support the clay) which is then covered with an oil and wax based plastilina clay.
This will then be scaled up to create the larger sculpture in the desired size. Fired ceramic clay may be used for portrait busts and seated figures not requiring an armature, but is less durable than bronze.
For Life-sized bronze pieces, a sturdy steel armature is welded to specifications enlarged from the maquette. This is then covered with a lightweight but very strong expanded polystyrene insulation foam, which is rasped, sawn and shaved to form the proportions of the sculpture. A thin covering of plastilina clay is applied over the polystyrene, which is then sculpted and detailed, ready for the rubber mold.
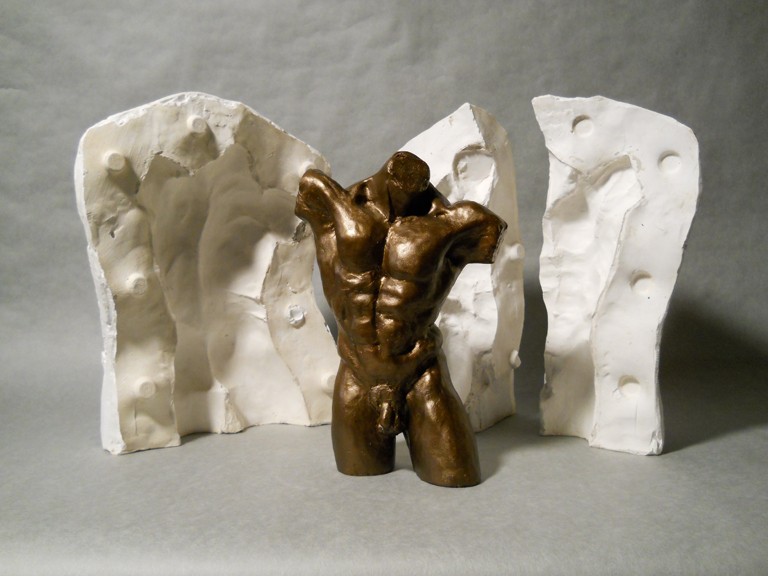
Mold Making
Plaster of Paris is often used in making molds from sculptures. Casts can be then poured or pressed into the mold using clay, cement, or wax. Unlimited copies can then be made this way.

For the making of bronze sculptures, multiple coats of mold rubber are brushed onto the clay sculpture, recording even the artist's fingerprints in the clay. this is later coated with layers of plaster of Paris and burlap in order to retain the form of the sculpture once it is removed from the flexible rubber mold. A special wax is melted and poured into the hollow mold, is rolled and rotated to reach all areas inside of the mold, and then allowed to cool for removal.
The Sprue System
Wax rods are heated and affixed to the hollow wax sculpture to later act as plumbing, enabling the molten bronze to be poured entirely into the form, and allowing the gases to escape.
The Ceramic Mold
The sprued wax sculpture is coated with multiple layers of a ceramic and sand mixture, drying between each layer. This mold is then fired in a burnout kiln to allow the wax to melt away, creating a hollow form that will be filled with the molten bronze. This "lost wax method of casting in bronze was developed in China over four thousand years ago!
The Pour
Bronze ingots are placed inside of a gas fired furnace and when melted, at about 2,000 degrees, is poured into the still hot ceramic mold. After cooling, the solid bronze is devested using chisels and pic hammers, destroying the mold.
Chasing and Finishing
After sand blasting the sculpture to remove excess mold material, many hours are spent removing the sprue system, de-burring, grinding, filing, and repairing any imperfections in the bronze. If the sculpture is cast in multiple pieces they are then welded together and again sand blasted.
The Patina
The sculpture is heated using an oxy-acetylene torch and at the same item receives a mixture of chemicals that are brushed or sprayed on. This gives the bronze a warm, slightly aged appearance in most cases. While still very hot, paste wax is brushed onto the sculpture to preserve and prevent further aging of the patina, and is then buffed to create a soft shine to the finish.
Base Mounting
Threaded rods or screws are secured to the bottom of the sculpture, which is then mounted on a wood or stone base. Life-sized works are usually permanently bolted into a cement or stone surface.